Precautions for cooperation between gear pump manufacturers and refineries
2025-04-21 11:16:25
During the cooperation between gear pump manufacturers and refineries, special attention should be paid to the following key issues to ensure equipment reliability, safety, and long-term cooperation efficiency:
1. Strictly match the working condition requirements
Medium characteristics: Clearly define the viscosity, corrosiveness (sulfur content), temperature range, and presence of particulate matter (such as catalytic cracking slurry) of the transported oil, and select corrosion-resistant materials (such as 316L stainless steel, Hastelloy alloy) or special coatings.
Pressure and flow rate: Accurately calculate the working pressure (considering pulsation effects) and flow rate according to the requirements of refining processes (such as conventional depressurization and hydrocracking), ensuring that there is a 10-15% margin for the rated parameters of the pump.
Sealing form: Double end mechanical seals and blocking liquid systems are preferred for high-temperature oil products, and API 682 standard seals are required for flammable and explosive working conditions.
2. Materials and Manufacturing Standards
Material certification: Material reports (such as ASTM A216 Gr. WCB) are required for the pump body and gears, and the gear hardness must reach HRC58-62 to resist abrasive wear.
API 676 compliance: Key operating conditions require compliance with API 676 standards (positive displacement pump standards), including performance test curves and vibration limits (such as ≤ 4.5mm/s RMS).
Special treatment: The gear surface can be treated with nitriding or hard chrome plating to enhance wear resistance.
3. Safety and Explosion proof Design
Explosion proof certification: Motors and electrical components must meet ATEX or IECEx Zone1 standards, with explosion-proof levels such as Ex d IIB T4.
Pressure relief protection: A safety valve must be installed at the outlet, with a set pressure not exceeding 10% of the maximum working pressure of the pump.
Static elimination: The grounding resistance of the pump body and pipeline should be less than 10 Ω to prevent static electricity accumulation.
4. Installation and maintenance collaboration
Alignment requirement: The alignment error of the coupling should be less than 0.05mm, and a laser alignment instrument should be used for calibration.
Pipeline design: It is recommended to have an inlet pipeline flow rate of 0.5-1.5m/s to avoid cavitation (NPSHa should be ≥ 1.3 × NPSHr).
Maintenance plan: Provide a maintenance checklist based on operating hours (such as replacing bearing grease every 2000 hours and using NLGI 2nd grade extreme pressure lithium grease).
5. Performance validation and data tracking
Factory testing: A third-party witnessed performance test report (including flow pressure curve and efficiency curve) is required.
Operation monitoring: It is recommended to install vibration sensors (such as SKF CMJB 100) and temperature probes, and connect the data to the DCS system.
Failure analysis: Establish MTBF (Mean Time Between Failures) index and conduct metallographic analysis on abnormally worn gears.
6. Business and Regulatory Compliance
Technical agreement: The gear pump manufacturer should specify the warranty period (recommended to be ≥ 18 months) and spare parts response time (such as 24 hours on-site in emergency situations).
HSE requirements: comply with OSHA 1910 or GB 50058 explosion-proof specifications, and provide SIL level certification (if required).
Logistics protection: During transportation, anti rust oil needs to be injected into the pump chamber, and anti-collision sleeves should be installed on the shaft extension end.
7. Special requirements for refineries
High temperature conditions: If the temperature exceeds 260 ℃, a water-cooled jacket or hot screen design is required.
Hydrogen containing environment: The material must meet the hydrogen embrittlement resistance requirements of NACE MR0175.
Switching media: Design a fast flushing interface to avoid cross contamination of oil products.
By strictly controlling the above technical details, the failure rate of gear pumps in refining units can be significantly reduced (target<1% annual failure rate), and the service life can be extended to more than 5 years. It is recommended that gear pump manufacturers conduct quarterly KPI evaluations (including leakage rate, energy consumption kWh/m ³, and other indicators) during the initial stage of cooperation.
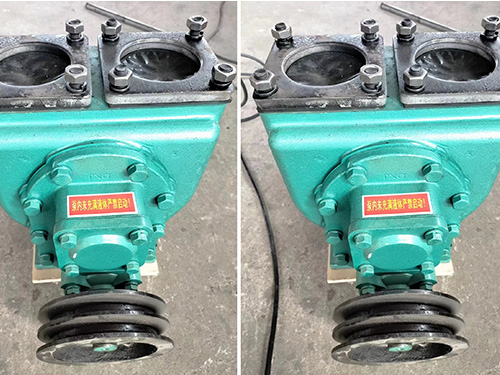
The YHCB high flow pump has the characteristics of large flow rate, high head, small settli...
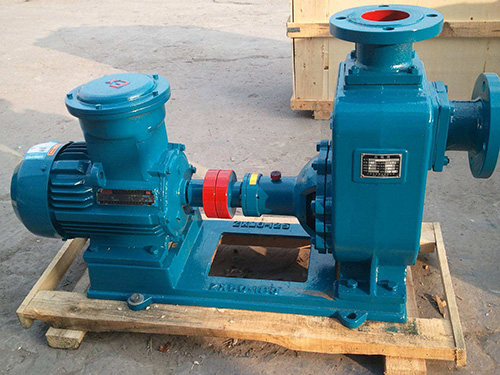
The CYZ centrifugal pump adopts an axial return liquid pump body structure, which is compos...
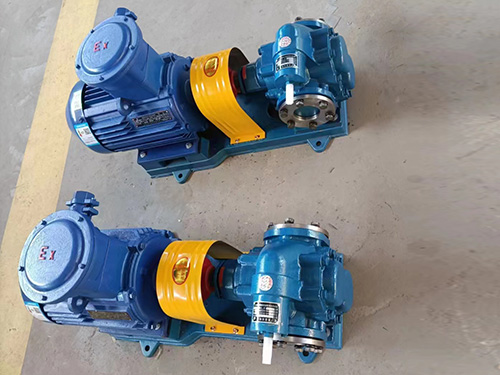
Copper gear pump (KCB type) is suitable for conveying lubricating oil or other liquids with...
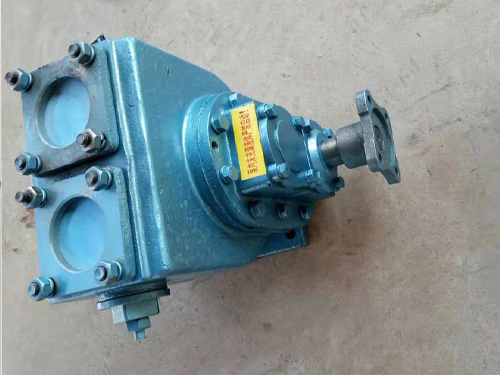
The car mounted circular arc gear pump can be installed on the car and driven by the output...