What sealing is required for gear pump to transport solvents
2025-02-20 08:09:21
When transporting solvents in gear pumps, selecting appropriate seals requires comprehensive consideration of solvent characteristics, working conditions, and safety requirements. The following are key selection factors and recommended solutions:
1. Selection of sealing type
(1) Mechanical seal (preferred)
Single end mechanical seal: Suitable for non hazardous, low volatility solvents, ensuring material resistance to chemical corrosion.
Double end mechanical seal (API 682 layout 2/3):
Recommended for toxic, flammable, or volatile solvents (such as acetone, toluene).
An isolation liquid system (such as PLAN 53/54) needs to be configured to form a double sealed barrier to prevent leakage.
Containerized mechanical seal : Easy to install, low risk of leakage, suitable for scenarios with high maintenance requirements.
(2) Packing seal (careful selection)
Only used for low-pressure solvents that are non hazardous and allow for trace leaks (such as room temperature clean water conditions), gear pumps require regular maintenance.
Not recommended for use with volatile or hazardous solvents.
2. Selection of sealing materials
(1) Sealing surface material
Silicon carbide (SiC): wear-resistant and corrosion-resistant, suitable for most solvents (including acids and bases).
Hard alloy (WC): High hardness, suitable for solvents containing particles.
Polytetrafluoroethylene (PTFE): resistant to strong corrosion (such as concentrated sulfuric acid and hydrofluoric acid), but has lower mechanical strength.
Alumina ceramics: an economical choice suitable for weakly corrosive solvents without particles.
(2) Elastic material
Fluororubber (FKM): resistant to oil and most solvents (avoid using for ketones and esters).
Perfluororubber (FFKM): resistant to strong chemical corrosion (such as strong acids, alkalis, ketones), with high cost.
PTFE coated O-ring: Compatible with almost all solvents, with a wide temperature range (-200 ° C to+260 ° C).
3. Adaptation to key operating conditions
High temperature solvent (>150 ° C):
Choose silicon carbide or hard alloy for the sealing surface, and use FFKM or graphite filler for the elastomer.
Containing particulate solvent :
Using hard to hard sealing surfaces (such as SiC vs SiC) to avoid wear of soft materials (such as graphite).
High pressure working condition:
Double end mechanical seal+balanced design, reducing the load on the sealing surface.
4. Auxiliary system configuration
Rinse Plan (API PLAN 11/21/32):
Cool the sealing surface and flush away impurities to extend its lifespan (such as flushing with clean liquid from the pump outlet for PLAN 11).
Isolation Fluid System (PLAN 53/54):
Double end sealing requires the injection of inert isolation fluid (such as glycerol or synthetic oil) to maintain the pressure in the sealing chamber.
5. Example of Common Solvent Sealing Solutions
Precautions
1. Compatibility testing : It is necessary to confirm the chemical compatibility between the sealing material and the solvent (refer to ASTM D471 standard).
2. Safety certification : Flammable solvents must comply with ATEX or API explosion-proof requirements.
3. Maintenance Monitoring : Install leak sensors and regularly check the isolation fluid pressure and sealing temperature.
If a more precise solution is needed, the sealing of the gear pump should be selected based on the specific solvent name, temperature, pressure, and particle content.
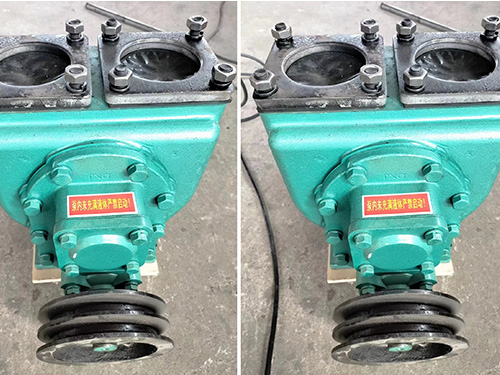
The YHCB high flow pump has the characteristics of large flow rate, high head, small settli...
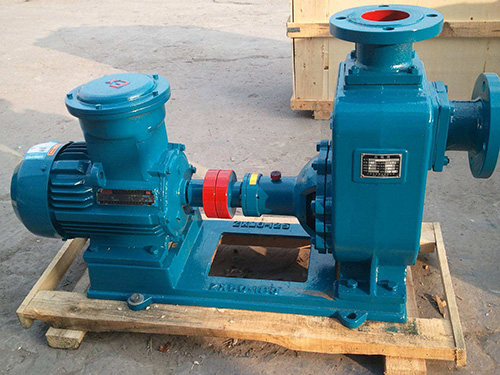
The CYZ centrifugal pump adopts an axial return liquid pump body structure, which is compos...
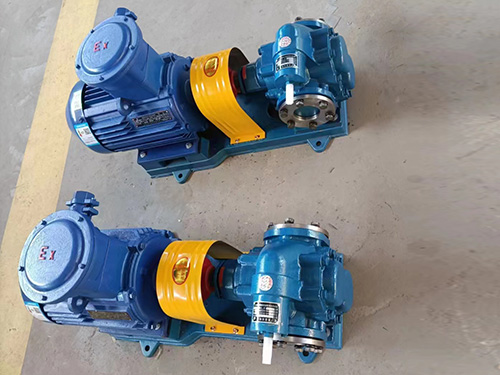
Copper gear pump (KCB type) is suitable for conveying lubricating oil or other liquids with...
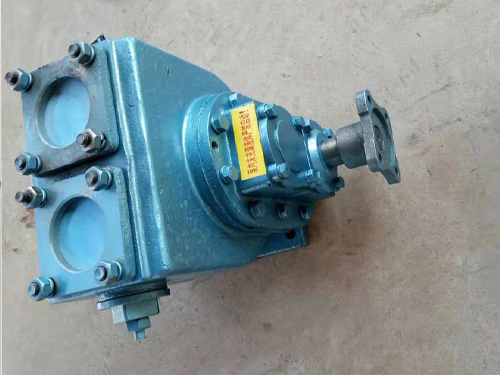
The car mounted circular arc gear pump can be installed on the car and driven by the output...