Advantages and disadvantages of high viscosity pumps and gear pumps compared to each other
2025-01-17 09:41:26
Comparative analysis of advantages and disadvantages between high viscosity pumps and gear pumps
Abstract: This article aims to explore in depth the performance characteristics of high viscosity pumps and gear pumps in industrial applications, and analyze in detail their respective advantages and disadvantages. By studying the working principles, structural characteristics, and practical application scenarios of two types of pumps, comprehensive and valuable reference basis is provided for pump selection decisions in related engineering fields, so as to select the most suitable pump type according to specific working conditions and achieve the best work efficiency and economic benefits.
1、 Introduction
In many industrial production processes, fluid transportation is a key link. Different types of pumps need to be adapted for fluids of different properties to ensure efficient and stable transportation. High viscosity pumps and gear pumps, as two common types of pumps, play an important role in handling fluids of various viscosities. Understanding their advantages and disadvantages is of great significance for optimizing industrial processes, reducing costs, and improving equipment reliability.
2、 High viscosity pump
(1) Working principle
High viscosity pumps typically operate based on the principle of displacement, periodically sucking and discharging high viscosity fluids by changing the volume of the working chamber. For example, screw pumps rely on the mutual meshing and rotation between screws to form a sealed chamber, which pushes the fluid to move along the axial direction.
(2) Advantages
1. High viscosity and strong adaptability: It can effectively transport fluids with a wide viscosity range, ranging from hundreds of centipedes to hundreds of thousands of centipedes. This makes it perform well in handling high viscosity media such as asphalt, ink, and rubber fluid, and can maintain stable flow output.
2. Stable flow rate: Due to its volumetric working mode, as long as the pump speed is stable, it can provide a relatively uniform and stable flow rate. This is very important for some production processes that require high flow accuracy, such as coating production, food processing and other industries, to ensure consistency in product quality.
3. Low shear force conveying: During the conveying process, high viscosity pumps apply relatively small shear forces to the fluid. This can prevent the material structure from being damaged and maintain its original properties for materials that are sensitive to shear, such as high viscosity fluids containing fibers or particles.
(3) Disadvantages
1. Complex structure: Some high viscosity pumps, such as screw pumps, require high precision in the manufacturing and assembly of their screws, resulting in a relatively complex overall structure. This not only increases the manufacturing cost of the equipment, but also makes maintenance more difficult, requiring professional technicians and tools.
2. High price: Due to its special design and high-precision manufacturing requirements, the procurement cost of high viscosity pumps is generally higher than some conventional types of pumps. This to some extent limits its application in some cost sensitive projects.
3. Limited applicable temperature range: The performance of materials and seals of high viscosity pumps may vary at different temperatures, so their applicable temperature range is relatively narrow. Excessive or insufficient temperature may affect the sealing and normal operation of the pump, requiring additional temperature control measures.
3、 Gear pump
(1) Working principle
Gear pump is also a type of positive displacement pump, mainly composed of a pair of meshing gears. When the gear rotates, the tooth groove space gradually increases at the suction end, forming negative pressure and sucking in the liquid; At the oil discharge end, the tooth groove space gradually decreases, and the liquid is squeezed and discharged.
(2) Advantages
1. Simple and compact structure: The structure of a gear pump is relatively simple, mainly composed of a few components such as gears, pump body, and shaft. This simple structure makes its manufacturing process mature, cost-effective, and easy to install and maintain.
2. Strong self-priming ability: Gear pumps have good self-priming performance, which can overcome the resistance in the suction pipeline to a certain extent and quickly suck liquid into the pump. This feature makes it suitable for situations that require quick start and frequent start stop.
3. Wide applicability: It can transport various types of fluids, including low viscosity and medium viscosity oil products, chemical raw materials, etc. And there are corresponding specifications of products to choose from under different pressure and flow requirements, with strong universality.
(3) Disadvantages
1. Large flow pulsation: Due to the intermittent meshing process of the gears, there is a certain degree of pulsation in the flow of the gear pump. This type of flow pulsation may cause system vibration and noise, which is not suitable for some processes that require extremely high flow stability.
2. Limited high viscosity performance: Although gear pumps can transport fluids of a certain viscosity, as the viscosity increases, the internal leakage will increase, leading to a decrease in pump efficiency and affecting the stability of flow rate and pressure. Compared to high viscosity pumps, their ability to handle high viscosity fluids is weaker.
3. Wear problem: Friction and wear between gear teeth are inevitable during high-speed operation. After long-term operation, gear wear can lead to increased clearance and leakage, which in turn affects the performance and service life of the pump. Regular replacement of vulnerable parts such as gears increases operating costs.
4、 Conclusion
In summary, high viscosity pumps and gear pumps each have their unique advantages and disadvantages. High viscosity pumps have significant advantages in handling high viscosity, shear sensitive fluids, and situations requiring stable flow rates, but they have shortcomings such as complex structure, high cost, and limited temperature adaptability; Gear pumps are widely used in many conventional fluid transportation systems due to their simple structure, strong self-priming ability, and wide applicability. However, their large flow pulsation, poor high viscosity performance, and wear issues also limit their use in certain specific operating conditions. In practical engineering applications, engineers need to comprehensively consider various factors such as fluid properties (such as viscosity, temperature, corrosiveness, etc.), flow and pressure requirements, system stability requirements, and cost, weigh the pros and cons, and choose the most suitable pump type to ensure efficient and reliable operation of the entire industrial production process. In the future, with the continuous advancement of technology, it is believed that high viscosity pumps and gear pumps will make greater breakthroughs in performance improvement, structural optimization, and better meet the diversified needs of industrial development.
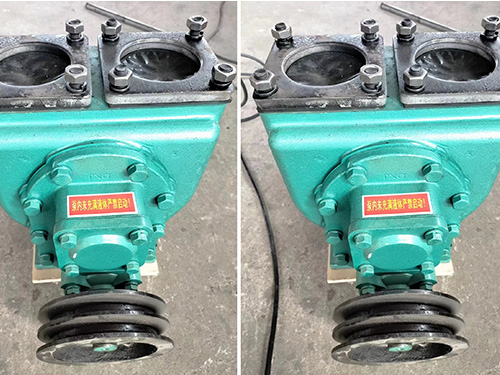
The YHCB high flow pump has the characteristics of large flow rate, high head, small settli...
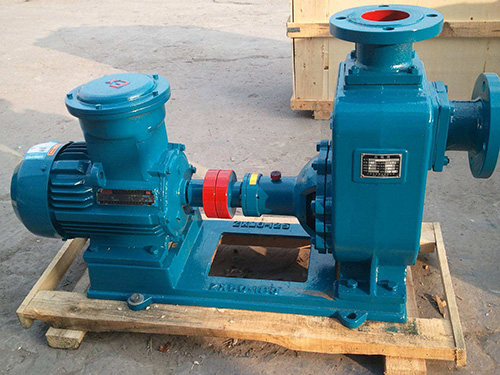
The CYZ centrifugal pump adopts an axial return liquid pump body structure, which is compos...
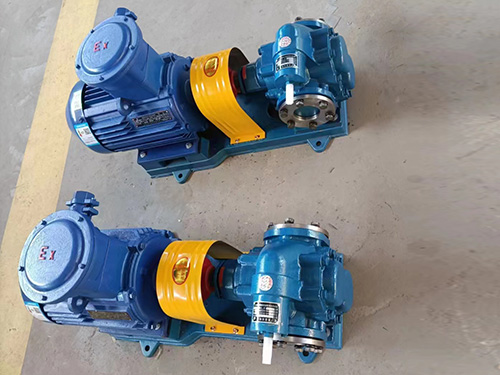
Copper gear pump (KCB type) is suitable for conveying lubricating oil or other liquids with...
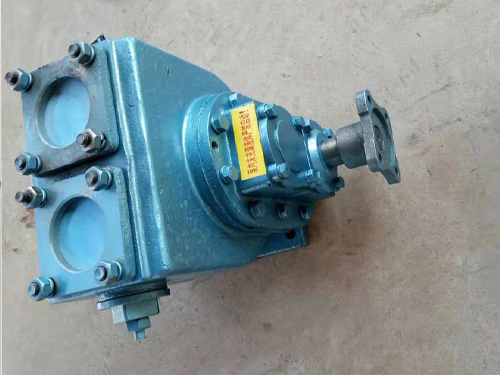
The car mounted circular arc gear pump can be installed on the car and driven by the output...