Solution and repair knowledge for vibration of petroleum gear pumps
2023-01-29 14:59:02
1、 The solution to gear pump vibration
Stainless steel oil pump mechanical vibration is inevitable in rotating equipment and flowing media. Therefore, in the manufacturing and installation process of the unit, the interference caused by vibration should be avoided as much as possible in the design, operation, and management of the unit, and the vibration hazards should be reduced to a minimum. When the gear pump or unit vibrates, the possible causes of the vibration should be analyzed one by one based on the specific situation, and the root cause of the problem should be identified before taking technical measures. Some measures are relatively simple, while others are quite complex. If a large amount of funds are required, a technical and economic comparison should be made between several feasible solutions, combined with the technical transformation of the unit. The following are common causes and measures for vibration in motors, gear pumps, and pump rooms
Common causes and measures of gear pump vibration:
1. Difficulty in manual turning: pump shaft bending, bearing wear, unit misalignment, impeller collision with pump casing.
. Measures: Straighten the pump shaft, adjust or replace bearings, recalibrate the concentricity of the unit, and readjust the clearance 2. Gear pump shaft swing is too large: bearings and journal wear or excessive clearance. Measures: Repair the journal, adjust or replace the bearings 3. Hydraulic imbalance: Impeller imbalance, blockage or damage of individual blade slots in centrifugal pumps. Measures: Recalibrate the static and dynamic balance of the impeller, block it, repair or replace the impeller 4. Excessive shaft power of axial flow pump: The water level in the inlet pool is too low, the impeller is not submerged enough, debris entangles the impeller, the degree of pump cavitation damage varies, and the impeller is damaged. Measures: Raise the water level of the inlet pool, lower the installation elevation of the water pump, set up debris barriers, and repair or replace the impeller 5. Foundation in vibration: Poor foundation stiffness or loose or resonant bottom screws. Measures: Strengthen the foundation and tighten the foundation screws 6. The efficiency of gear pump units sharply decreases or the efficiency of axial flow pump units slightly decreases, accompanied by cavitation noise. Measures: Change the speed of the water pump, avoid the resonance area, identify the cause of cavitation, and take measures to prevent cavitationVibration of the unit caused by other reasons and measures:
1. Blockage of the trash rack and decrease in the water level of the inlet water tank.
. Measures: Clean up the trash rack and install a trash rack cleaning device 2. The design of the front pool and inlet pool is unreasonable, and the inlet flow channel is not matched with the pump, which worsens the inlet conditions. Measures: Clean up the trash rack and install a trash rack cleaning device. Reasonably design the inlet pool, inlet pool, and inlet flow channel 3. The formation of siphon takes too long, causing the unit to operate for a long time under non design conditions. Measures: Install a vacuum pumping device and design and improve the siphon type water outlet channel reasonably 4. The inlet pipeline is not firmly fixed or causes resonance. Measures: Install pipeline anchor blocks and support blocks, reinforce pipeline supports, change operating parameters, and avoid resonance zones by changing operating parameters 5. Repeatedly hitting the door seat or closing the door with excessive impact force. Measures: Install exhaust holes in front of the outlet of the flow channel (or pipeline), design the flap door reasonably, and take control measures to reduce the impact force when the flap door is closed 6. Sharp pressure changes and water hammer effects in the outlet pipeline. Measures: Other measures to prevent water hammer, such as slow closing valves and pressure regulating wells 7. The starting and stopping sequence of the gear pump unit is unreasonable, resulting in a deterioration of the water pump inlet conditions. Measure: Optimize the sequence of startup and shutdown2. Common Knowledge of Gear Pump Repair
With the increase of usage time, gear pumps may experience problems such as insufficient pump oil or even failure to pump oil, mainly due to excessive wear and tear on the relevant parts.
. The wear parts of the gear pump mainly include the driving shaft and bushing, the center hole and shaft pin of the passive gear, the inner cavity of the pump housing and the gear, the gear end face and the pump cover, etc. When the main technical indicators of the lubricating oil pump fail to meet the requirements after wear, it should be disassembled and separated, the worn parts and degree should be checked, and corresponding measures should be takenFirstly, after the wear of the driving shaft and bushing, the clearance between the driving shaft and bushing in the gear pump will increase, which will inevitably affect the pump oil volume.
. In this case, the method of repairing the driving shaft or bushing can be used to restore its normal fit clearance. If the wear of the driving shaft is slight, simply press out the old bushing and replace it with a standard size bushing, and the clearance can be restored to the allowable range. If the wear between the driving shaft and the bushing is severe and the fit gap exceeds the standard, not only should the bushing be replaced, but the driving shaft should also be increased in diameter by chrome plating or vibration welding, and then ground to the standard size to restore the fit requirements with the bushing
Secondly, repair of lubricating oil pump housing cracks: The housing cracks can be repaired by welding with 508 nickel copper welding rods. The weld seam must be tight and have no pores, and the flatness error of the joint surface with the pump cover should not exceed 0.05 millimeters Repair of wear on the driving shaft bushing hole and the driven shaft hole: After the driving shaft bushing hole is worn, the wear marks can be obtained by reaming, and then a bushing enlarged to the corresponding size can be used. The wear of the driven shaft hole is also marked by the hinge cutting method, and then the repair of the inner cavity of the driven shaft pump housing is prepared according to the actual size of the hinge cut hole. After the inner cavity of the pump housing is worn, the inner cavity embedding method is generally adopted, which is to enlarge the inner cavity and insert cast iron or steel bushings. After inserting the sleeve, polish the inner cavity to the required size and grind off the liner that extends out of the end face to make it flush with the pump casing joint surface Repair of valve seat: There are two types of pressure limiting valves: spherical valves and plunger valves. After the spherical valve seat is worn out, a steel ball can be placed on the valve seat, and then gently tap the steel ball with a metal rod until the ball valve is tightly fitted with the valve seat. If the valve seat is severely worn, it can be first reamed to remove the wear marks, and then the above method can be used to make it tight. After the plunger valve seat is worn, a small amount of valve sand can be added for grinding until it is tightly fittedThird, Repair of Pump Cover
Repair of Working Surface: If the wear on the working surface of the pump cover is relatively small, manual grinding can be used to remove the wear marks. That is, a small amount of valve sand can be placed on the platform or thick glass plate, and then the pump cover can be ground on top until the wear marks and the working surface are flat.
. When the wear on the working surface of the pump cover exceeds 0.1 millimeters, the method of turning first and then grinding should be adopted Repair of the drive shaft bushing hole: The repair method for the wear of the drive shaft bushing hole on the pump cover is the same as that for the wear of the drive shaft bushing hole on the housingFourth, the flipping of gears
Gear pump gear wear is mainly in the tooth thickness area, while the wear on the gear end face and tooth tip is relatively light.
. Gears have unilateral wear in the tooth thickness area, so they can be flipped 180 degrees for use. When the gear end face is worn, the end face can be ground flat, and the joint surface of the lubricating oil pump housing can be ground at the same time to ensure that the gap between the gear end face and the pump cover is within the standard range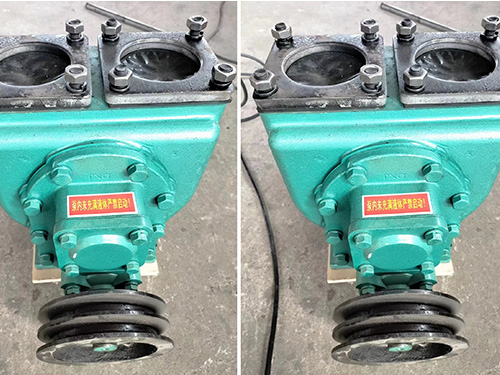
The YHCB high flow pump has the characteristics of large flow rate, high head, small settli...
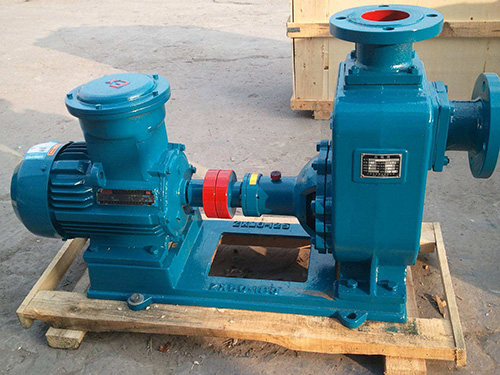
The CYZ centrifugal pump adopts an axial return liquid pump body structure, which is compos...
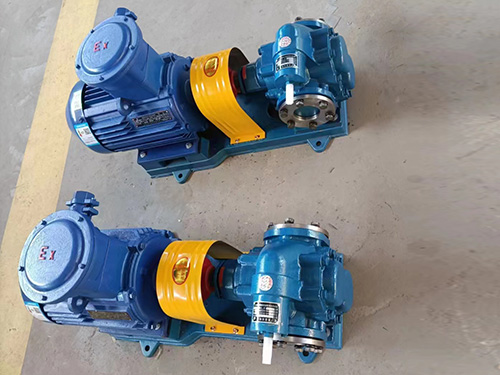
Copper gear pump (KCB type) is suitable for conveying lubricating oil or other liquids with...
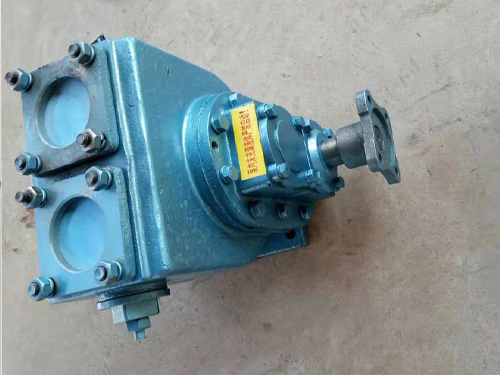
The car mounted circular arc gear pump can be installed on the car and driven by the output...