Pipeline pressure sealing technology and its main functions
2023-04-22 18:56:23
(1) Gear pump pipeline pressure sealing technology
Gear pump pipeline leakage occurs during oil transportation operation. To avoid hot work, pressurized sealing technology can be used. The basic principles and operating procedures are now introduced as follows
1. Pressure sealing principle
The pressure sealing technology for stainless steel oil pump pipelines is to apply an external thrust greater than the pressure of the medium in the system to a thermoplastic and thermally cured sealant under dynamic conditions of the fluid medium, so as to press it into and fill the sealing space composed of the fixture and the outer surface of the leakage site, blocking the leakage pores and channels of the pipeline.
. And this type of sealant, after delaying time and obtaining temperature, first becomes a plastic body and then reaches solidification, establishing a fixed new sealing structure at the leakage site to balance with the leakage medium, thereby cleaning up the leakage of the medium inside the pipe2. Operating Principles
(1) Survey the leakage site and determine the sealing implementation plan
In the implementation plan, the selection of sealing agent types, design and processing of fixtures that are suitable for the site, and arrangement of operation sequences must all be carried out through on-site investigation and arrangement.
. At the same time, it is necessary to understand the properties of the leaking medium, the temperature and pressure of the system; Measure the shape and size of the leaking area and develop preventive measures to be taken during the implementation process(2) Install fixtures at the leakage area
Place the fixtures with pre installed injection valves on the leakage area. There should be more than one injection valve, and the number should be conducive to the injection of sealant and the discharge of air.
. There must be a connection gap between the fixture and the outer surface of the leakage area. During operation, it is strictly prohibited to hit fiercely. When striking, copper rods and hammers should be used to prevent sparks from causing fire and explosion(3) Implement sealing operation
After confirming that the fixture is installed properly, connect the injection cylinder of the high-pressure injection tool to the injection valve, fill the selected sealing agent in the cylinder, connect the plunger and hydraulic cylinder, and then connect the high-pressure injection tool to the hand pressure oil pump with a high-pressure hose to perform the sealing agent injection operation.
During operation, inject sealant from the injection valve away from the leakage point and gradually move towards the leakage point until the leakage is cleared. During the injection process, special attention should be paid to controlling pressure, temperature, and the amount of sealant injected3. Several Key Issues in Implementation
Firstly, the design of the fixture is the key to implementing pressurized plugging.
. The function of the fixture is to contain the injected sealant and maintain the sealing force of the sealant, in order to achieve successful pressure sealing and sealing performance. Different forms of fixtures should be designed for different occasions and shapes, such as elbows, tees, straight pipes, etc. The strength of the fixture should also be designed to adapt to the pressure of the leaking medium. From this, it can be seen that the quality of fixture design directly affects the success or failure of sealing and the length of its service life, as well as the length of pressure sealing operation time and the amount of sealant consumed Secondly, the correct selection of sealant is another key factor in the success or failure of pressurized plugging. Due to the variety of production media and oil products, different types of oil products require the selection of sealants with different "heat curing" properties that are suitable for them. The selection of these sealants is based on physical and chemical indicators such as curing rate, medium resistance to dissolution, etc(II) Main function of gear pump valve
The main function of stainless steel pump valve is to prevent blockage of the outlet pipeline of the gear pump or high outlet pressure of the gear pump, which may cause the gear pump motor to burn out or damage the pipeline equipment.
. Choosing a gear pump requires pre calculating the required outlet pressure, also known as the head of the gear pump. Measure the actual operating pressure of a gear pump based on its actual working pressure, medium viscosity, and medium specific weight. In the operation experiment of the pump, the valve pressure of the gear pump is pre-set by adjusting the adjusting bolts of the gear pump valve. The main function of the pre adjusted pressure of the gear pump valve is to automatically open the pump valve when the pump outlet pipeline is blocked during normal operation, exceeding the pre-set pressure. At this time, the conveying medium of the gear pump will automatically circulate in the gear pump, thereby automatically releasing pressure, protecting both the gear pump and the motor from overload. Gear pumps equipped with valves mainly include KCB gear pumps, YCB arc gear pumps, stainless steel gear pumps, and high-temperature gear pumps Gear pumps and arc gear pumps are machinery used to increase liquid energy and belong to fluid machinery. They convert the mechanical energy of the prime mover into the energy of the conveyed liquid, achieving the purpose of conveying liquid and increasing liquid pressure There are 3000 gear pump manufacturers in China, accounting for one of the world's; The annual output value of gear pumps in China is about 22 billion yuan, which also accounts for one of the world's; The annual output value of gear pump enterprises is 5 billion yuan, accounting for 22% In today's world, the production of gear pump products is second only to motors, and they are widely used in agricultural drainage, urban and industrial water supply and drainage, thermal power plants, oil refineries, oil pipelines, factories, steel plants, shipyards, food and brewing, etc. It can be said that wherever liquid needs to flow, gear pumps are working In addition to using gear pumps to transport low viscosity liquids such as water, alcohol, gasoline, diesel, etc., various high viscosity lubricants, greases, petroleum, crude oil, residual oil, asphalt, paint, ink, animal and vegetable oil, honey, syrup, jam, cream, adhesive, toothpaste, coating, soap, paraffin, nylon, polyester, polyethylene and other plastics and rubbers in high-temperature liquid state during the production process, as well as various multiphase media such as cement slurry and mineral powder slurry during pipeline transportation, the application range of using gear pumps is increasing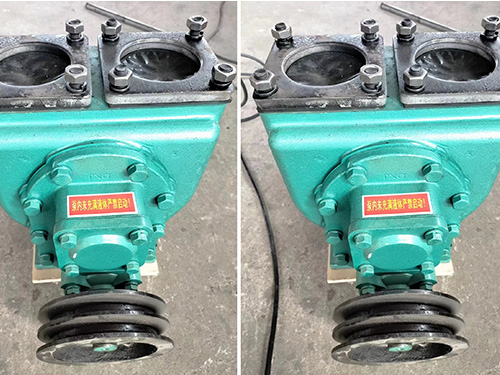
The YHCB high flow pump has the characteristics of large flow rate, high head, small settli...
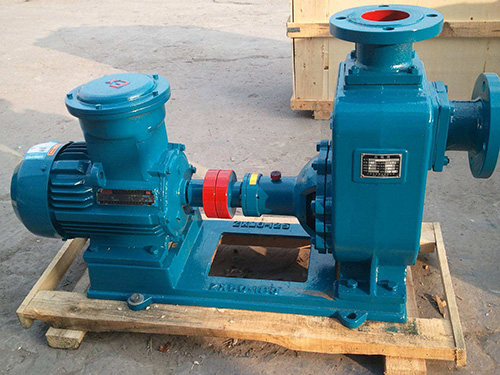
The CYZ centrifugal pump adopts an axial return liquid pump body structure, which is compos...
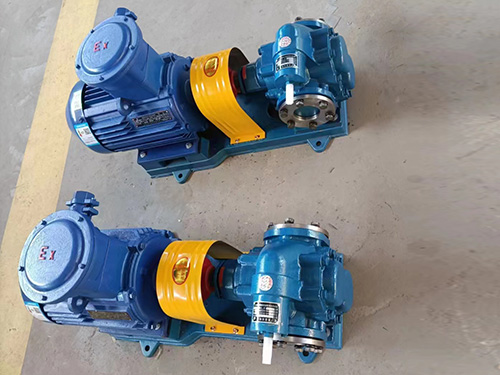
Copper gear pump (KCB type) is suitable for conveying lubricating oil or other liquids with...
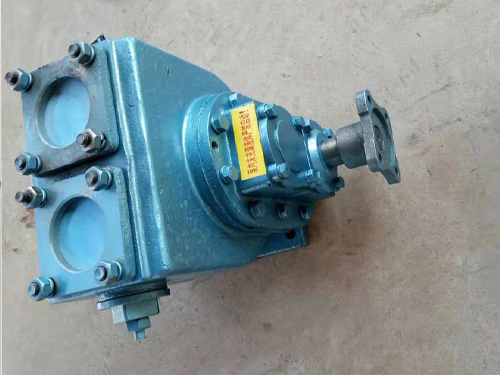
The car mounted circular arc gear pump can be installed on the car and driven by the output...