The application of petrochemical gear pumps in special situations and the main reasons for motor overheating
2023-04-06 13:32:47
(1) The application of gear pumps in certain situations: As viscosity increases, centrifugal pumps become inefficient, and users need to consider using positive displacement pumps (PD pumps, also known as positive displacement pumps). When the pressure needs to increase, some positive displacement pumps are difficult to sustain. When the temperature rises, other pumps will also fail
The stainless steel gear pump has two meshing gear shafts of the same size. The drive shaft is connected to the motor or reducer (through an elastic coupling) and drives another shaft. In heavy-duty industrial gear pumps, the gears are usually integrated with the shaft (as a component), and the tolerance of the shaft neck is very small There are three commonly used gear forms: straight teeth, helical teeth, and herringbone teeth. These three forms each have their own advantages and disadvantages, and have different applications Straight teeth are a simple form and are preferred for use under high-pressure conditions, as they do not have axial thrust and have higher conveying efficiency. The helical teeth have less pulsation during the conveying process and are quieter at higher speeds because the meshing of the teeth is gradual. However, due to the effect of axial thrust, the selection of bearing materials may result in limited inlet and outlet pressure differences and lower processing viscosity. Because axial force will push the gear towards the bearing end face and cause friction, only by selecting a bearing material with higher hardness or designing on its end face can we cope with this axial thrust The operating principle of an external gear pump is very simple. The liquid enters the suction end of the pump, is sucked in by the unmeshed interdental cavity, and then driven inside the interdental cavity to reach the outlet end along the outer edge of the gear shaft. The re meshing teeth push the liquid out of the cavity and into the back pressure area(2) The main reasons for the overheating of the gear oil pump motor
The selection of the oil pump motor is very important. Improper selection can lead to the phenomenon of motor overheating, even burning the motor. How to analyze the reasons for the overheating of the gear oil pump motor mainly includes several aspects.
, Motor shaft power gear oil pump configuration motor design requirements: Select a suitable motor according to the series spectrum, and the medium density exceeds that of the gear oil pump configuration motor: Configure a suitable gear oil pump motor
3. If the packing gland is pressed too tightly or the mechanical seal spring is adjusted too tightly: readjust the compression amount of the gland or mechanical seal spring
4. Poor pump assembly, friction or non concentricity between the motor and pump shaft: Check the assembly and eliminate assembly faults
Based on the above conditions, analyze one by one to find the cause of motor overheating, and repair the gear oil pump according to the corresponding fault cause.
What are the main reasons for mechanical seal leakage in gear oil pumps The problem of mechanical seal leakage in gear pumps and gear oil pumps has always been a major concern for customers. Due to the wide variety of mechanical seals available in the market, we will now explain one by one the situations of mechanical seal leakage in commonly used gear oil pumps in our daily lives. I hope it will be helpful for future customers who choose gear oil pumps or are currently using gear oil pumps! The mechanical seals used in conventional KCB gear oil pumps or YCB arc gear pumps are EX series or FOED series. The dynamic and static rings of these two types of mechanical seals are all made of a combination of graphite to graphite or graphite to silicon carbide without customer requirements. These two types of mechanical seals can only be used for conveying media with lubricating properties and temperatures not exceeding 100 ℃ due to material limitations (these two materials are not suitable for conveying lubricating grease, etc.). However, customers often do not understand these specific situations, so some customers choose gear oil pumps with mechanical seals that do not transport lubricating media, which can cause mechanical seal leakage. Alternatively, if the customer's conveying medium is corrosive or contains a small amount of solid particles, choosing a conventional mechanical seal will result in rapid wear of the dynamic or static rings of the mechanical seal, leading to gear oil pump leakage. Or it may be due to the corrosive nature of the medium being transported, causing premature damage to the O-ring seal on the mechanical seal, resulting in mechanical seal leakage of the gear oil pump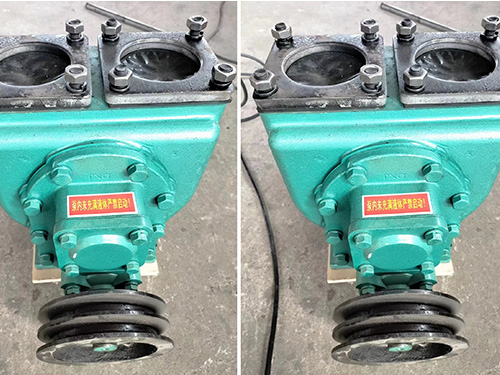
The YHCB high flow pump has the characteristics of large flow rate, high head, small settli...
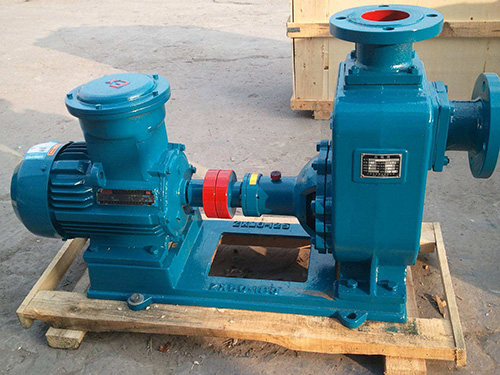
The CYZ centrifugal pump adopts an axial return liquid pump body structure, which is compos...
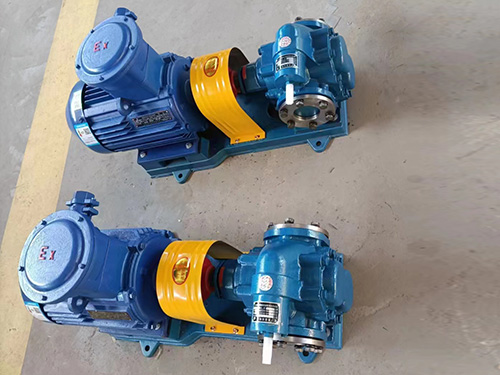
Copper gear pump (KCB type) is suitable for conveying lubricating oil or other liquids with...
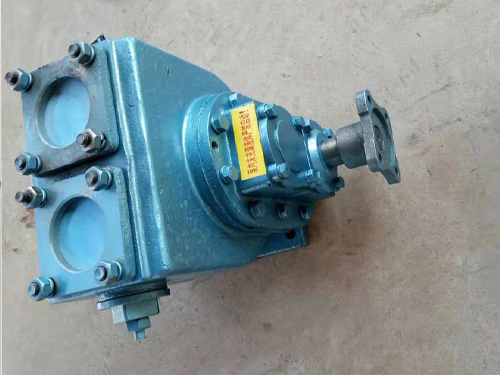
The car mounted circular arc gear pump can be installed on the car and driven by the output...