Function and maintenance precautions of petroleum stainless steel gear pump
2023-03-06 15:01:48
(1) 1. The stainless steel gear pump has a simple and compact structure, making it easy to use and maintain
2. The stainless steel gear pump has outstanding self suction performance, so it is not necessary to fill liquid before starting the pump each time 3. The smoothness of stainless steel gear pumps is achieved by actively transporting the liquid, so there is no need to add additional lubricant during normal operations 4. Using elastic couplings to transmit energy can compensate for small errors caused by equipment operation. When encountering unavoidable hydraulic impacts during pump operation, it can play an outstanding buffering role The hydraulic system consists of important components such as oil tank, stainless steel gear oil pump, pipeline, control valve, and hydraulic cylinder. During the operation of the hydraulic system, due to the forging of the internal oil channels of various control valves, the sticky sand attached to the interior falls off due to the action of pressure oil and other elements, resulting in contamination of the hydraulic system. At the same time, welding slag in the fuel tank and pipelines, internal burrs and burrs in the hydraulic cylinder are also factors that cause contamination of the hydraulic system. After the hydraulic system of the stainless steel gear pump is contaminated, the friction between the conflicting pairs of the gear pump intensifies, the sealing effect is ineffective, and then the oil seal of the gear pump is broken down and oil leakage occurs. Therefore, it is necessary to carry out cleaning of the valve body, oil tank and hydraulic accessories, as well as cleaning of the hydraulic cylinder, to ensure the cleanliness of the hydraulic system. COD in industrial wastewater, after secondary treatment, is directly discharged into the water body or enters the sewage treatment plant, which will form toxic and difficult to degrade substances in the receiving water body, leading to the growth of microorganisms and water active animals, ultimately endangering the self purification ability of the water environment and the deformation and operation of the sewage treatment plant. And using BAF as a pre-treatment skill for ultrafiltration can improve the function of the membrane and effectively reduce membrane infection. Li Kuixiao and others used BAF skills to treat the secondary biochemical treatment effluent of a sewage treatment plant in a certain city Biological Aerated Filter (BAF) is a new type of biofilm wastewater treatment technique that integrates physical filtration, chemical adsorption, and biological processes, which is environmentally friendly, economical, and energy-saving. In the field of industrial wastewater treatment, the microorganisms, chaotic biological species and structures, and outstanding wastewater interception and filtration capabilities in BAF make it widely used in industrial wastewater treatment. Biological Aerated Filter (BAF) is a new type of biofilm wastewater treatment technology that integrates physical filtration, chemical adsorption, and biological processes, which is environmentally friendly, economical, and energy-saving. In the field of industrial wastewater treatment, the microorganisms, chaotic biological species and structures, and outstanding wastewater interception and filtration abilities in BAF make it widely used in industrial wastewater treatment. The particle size of the filler has an impact on the treatment efficiency and operating cycle of BAF. The smaller the particle size of the filler, the better the treatment effect. However, when the particle size of the filler is small, the filter is prone to clogging, and the operating cycle is definitely short. Frequent backwashing is required, and it is not easy to play the role of the deep layer of the filler. The density of the filler is related to the strength of the backwash brush in the biofilter. The higher the density, the stronger the backwash brush strength, and the greater the energy consumption required(2) Maintenance precautions for magnetic gear pump
1) The shaft of the magnetic gear pump is broken.
. The pump shaft of the oil pump is generally made of 45 steel or 40Cr, as well as 304, 316, and 316L stainless steel materials. The main reason for the pump shaft breaking is that the shaft is twisted and broken due to the dry wear of the bearings during pump operation. When disassembling the pump for inspection, it can be seen that the bearings are severely worn. The main way to prevent the pump from breaking is to avoid idling the pump 2) The bearing of the magnetic gear pump is damaged. The bearings used in this shift of KCB Magnetic are made of silicon carbide or ceramic materials. If the pump runs out of water or there are impurities inside the pump at high temperatures, it will cause damage to the bearings. If the coaxiality requirement between the inner and outer magnetic rotors of the cylindrical coupling is not met, it will directly affect the service life of the bearing 3) The magnetic gear pump cannot produce liquid. The inability of a magnetic pump to produce liquid is a common malfunction of the pump, and there are many reasons for this. First, check if there is any air leakage in the suction pipeline of the pump, check if the air inside the suction pipeline is discharged, whether the amount of liquid filled in the magnetic pump is sufficient, whether there is any debris blocking the suction pipe, and also check if the pump is reversed (especially after replacing the motor or repairing the power supply line). Also, pay attention to whether the suction height of the pump is too high. If the above inspection still cannot solve the problem, the pump can be disassembled for inspection to see if the pump shaft is broken. The dynamic and static rings of the pump should also be checked for integrity, and the entire rotor should be able to move slightly axially. If axial movement is difficult, check if the carbon bearing is too tightly combined with the pump shaft It is worth noting that the magnetic pump has been repaired several times and no problems have been found. It is important to pay attention to whether the magnetic coupling is working properly. Bearings, inner magnetic rotors, and spacers all generate heat during operation, which will increase the working temperature. On the one hand, it will reduce the transmitted power, and on the other hand, it will cause great trouble for magnetic pumps that transport easily vaporized liquids. The power transmitted by a magnetic steel decreases continuously with the increase of temperature. Generally, the decrease in its transmission capacity is reversible below the working temperature of the magnetic steel, while it is irreversible above the temperature. That is, after the magnetic steel cools down, the lost transmission capacity can no longer be restored. When the magnetic coupling slips (loses step), the eddy current heat in the spacer will increase sharply, and the temperature will rise sharply. If not handled in a timely manner, it will cause demagnetization of the magnetic steel, leading to the failure of the magnetic coupling. Therefore, a cooling system should be designed for magnetic pumps. For media that are not easy to vaporize, the cooling circulation system generally leads out the liquid flow from the impeller outlet or pump outlet, and returns to the suction port through the bearing and magnetic transmission part. For media that is easy to vaporize, a heat exchanger should be added or the liquid flow should be directed to the storage tank outside the pump to prevent heat from returning to the suction port. For media with solid or ferromagnetic impurities, filtration should be considered. For high-temperature media, cooling should be considered to ensure that the magnetic coupling does not exceed the working temperature. When considering whether the speed is sufficient, the motor's own speed should be checked first, and a tachometer can be used to measure it. If the motor rotates normally, the possibility of slipping of the magnetic coupling can be considered 4) Insufficient head. The causes of this malfunction include: air in the conveying medium, damaged impeller, insufficient rotational speed, excessive specific gravity of the conveyed liquid, and excessive flow rate 5) Insufficient traffic. The main reasons for insufficient flow are: impeller damage, insufficient speed, high head, and blockage of debris inside the pipe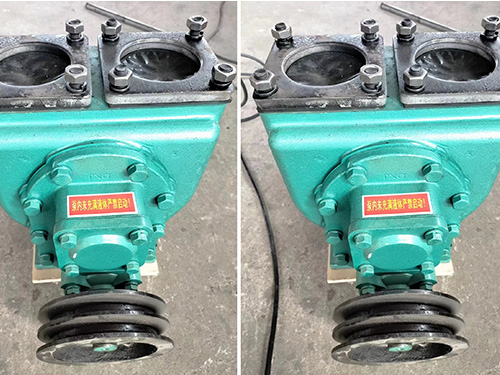
The YHCB high flow pump has the characteristics of large flow rate, high head, small settli...
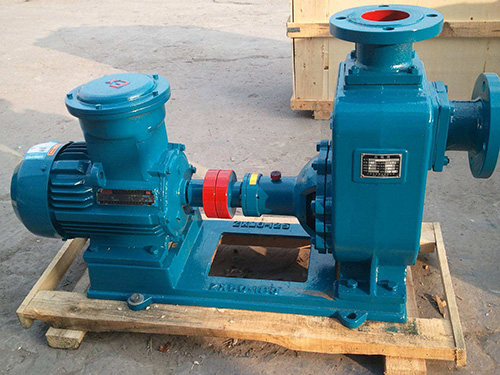
The CYZ centrifugal pump adopts an axial return liquid pump body structure, which is compos...
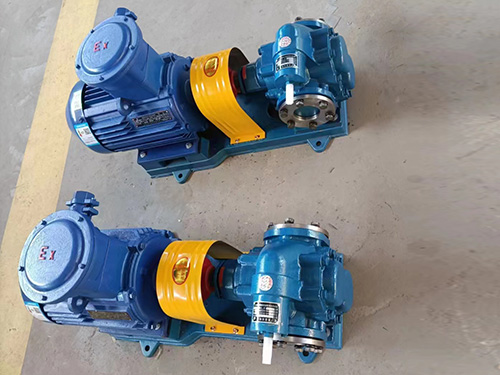
Copper gear pump (KCB type) is suitable for conveying lubricating oil or other liquids with...
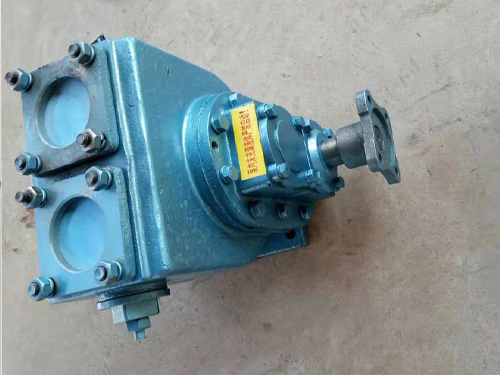
The car mounted circular arc gear pump can be installed on the car and driven by the output...