Maintenance and installation issues of petrochemical gear oil pumps
2023-07-02 14:41:21
[1] Maintenance of Petrochemical Arc Pump Equipment maintenance personnel mainly rely on the actual operating time of the arc pump equipment during maintenance. In general, after the operating time of small-scale pump equipment reaches 240 hours, a primary maintenance operation needs to be carried out. After the accumulated working time reaches 720 hours, a secondary maintenance operation needs to be started. After reaching 1000 hours, maintenance should begin. However, large circular arc pump equipment is different from small circular arc pump equipment, with a cumulative operating time of 1000 hours for primary maintenance, 3000 hours for secondary maintenance, and 10000 hours. When maintenance personnel carry out maintenance, they mainly include the following aspects
Firstly, technicians need to inspect the appearance of the equipment for any issues, including all exposed parts and the transmission structure of the equipment. Secondly, technicians need to check the condition of the transmission structure to determine if there is any looseness or corrosion in the structure. If there are loose positions, tools should be used for reinforcement. In addition, the wear of the bearing parts of the circular gear oil pump transmission structure should be checked. If the wear is too severe, components should be replaced in a timely manner. 3、 Technical personnel need to check the lubrication of the equipment, including various indicators of lubricating oil testing, status detection of oil filters, and other issues. After checking for accuracy, the oil level should be observed. If the oil level is insufficient, it should be replenished in a timely manner. If there are problems with the quality of lubricating oil, it should also be replaced and not used again to prevent leakage and blockage during subsequent operation. 4、 Technicians should carefully inspect the electrical system of the connected equipment. In order to maintain the cleanliness of the motor, they should frequently use cleaning tools to wipe the motor equipment. In addition, it is necessary to check the wiring ports between the motor and the cable for any poor contact. Afterwards, the insulation and grounding devices of the circuit should be inspected[2] Installation problems of mechanical seals for circular arc gear pumps
1. The greater the spring compression, the better the sealing effect.
Excessive spring compression can cause sharp wear or instantaneous burning of the friction pair; It will also cause the spring to lose the ability to adjust the end face of the moving ring, leading to the failure of the sealing of the circular gear pump 2. The tighter the sealing ring of the moving ring, the better Tight sealing ring of the moving ring is not beneficial. One is to intensify the wear between the sealing ring and the shaft sleeve, leading to premature leakage; Secondly, it increases the resistance to axial adjustment and movement of the moving ring, making it difficult to make timely adjustments when the working conditions change frequently; Thirdly, the spring is prone to damage due to excessive fatigue; The fourth is to deform the sealing ring of the moving ring, which affects the sealing effect 3. The tighter the static ring seal, the better The static ring seal is basically in a static state, and the sealing effect is better when it is relatively tight, but it is also possible to be too tight. One is that the static ring seal is excessively deformed, which affects the sealing effect; The second is that the material of the static ring is mostly graphite, which is generally brittle and can easily cause fragmentation under excessive stress; The third difficulty is installation and disassembly, which can easily damage the static ring 4. The tighter the impeller lock nut, the better In mechanical seal leakage, leakage between the shaft sleeve and the shaft (inter shaft leakage) is quite common It is generally believed that inter shaft leakage is caused by the impeller lock nut not being tightened. In fact, there are many factors that can lead to inter shaft leakage, such as the failure of the inter shaft sealing gasket, deviation, impurities, significant positional errors at the fit between the shaft and the shaft sleeve, damage to the contact surface, excessive clearance between various components on the shaft, and excessive thread length at the shaft head, all of which can cause inter shaft leakage. Excessive locking of the lock nut will only lead to premature failure of the shaft gasket. On the contrary, moderately locking the lock nut will maintain the compression elasticity of the shaft gasket. During operation, the lock nut will automatically lock in a timely manner, ensuring that the shaft gasket is always in a good sealing state 5. Disassembling and repairing is always better than not disassembling Once there is a mechanical seal leakage in the circular gear pump, it is urgent to disassemble and repair it. In fact, sometimes the seal is not damaged, and only adjusting the working condition or adjusting the seal appropriately can leak. This not only avoids waste but also verifies one's fault diagnosis ability, accumulates maintenance experience, and improves maintenance quality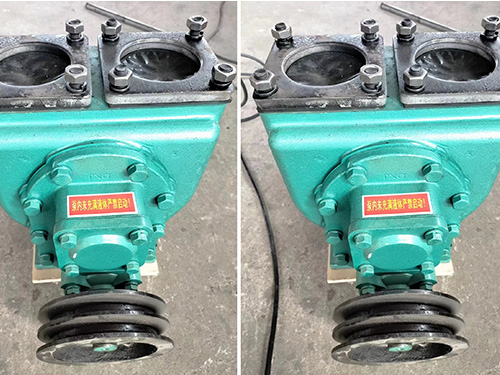
The YHCB high flow pump has the characteristics of large flow rate, high head, small settli...
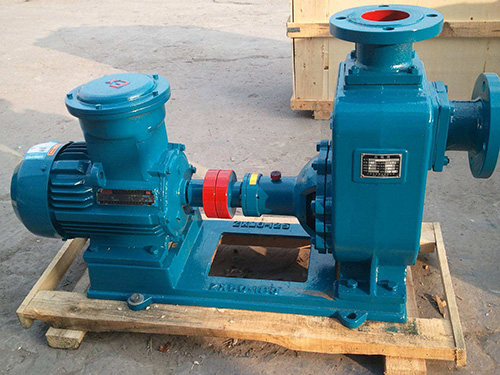
The CYZ centrifugal pump adopts an axial return liquid pump body structure, which is compos...
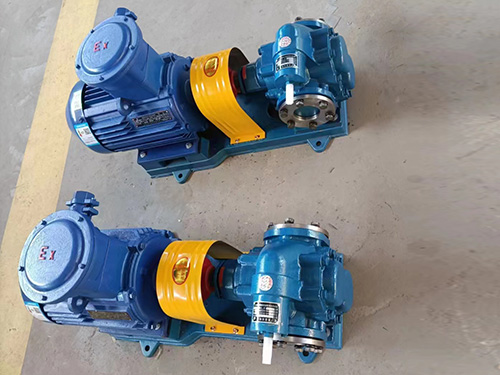
Copper gear pump (KCB type) is suitable for conveying lubricating oil or other liquids with...
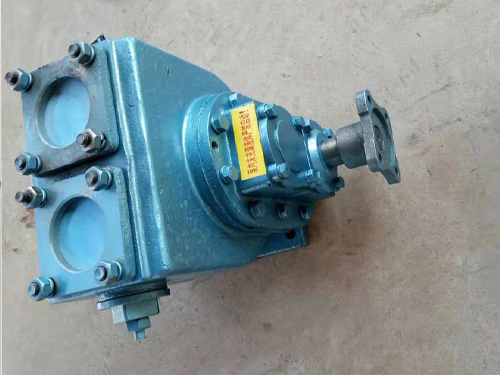
The car mounted circular arc gear pump can be installed on the car and driven by the output...