How can petrochemical improve the service life and leakage treatment of gear pumps
2023-02-10 14:59:42
【1】 How can we improve the service life of gear pumps
Stainless steel pumps play a very important role in industrial production processes. How to improve the service life of gear pumps, make them play a significant role in production, and minimize the occurrence of gear pump failures? Below, our company's experts in the gear pump industry will explain to you Firstly, from the material differentiation of gear pumps, gear pumps are mainly divided into ordinary cast iron gear pumps, stainless steel gear pumps, high-temperature gear pumps, and copper gear pumps. Divided into high-temperature gear pumps, insulated gear pumps, and magnetic driven gear pumps in terms of structure and performance. For conveying under different working conditions, the material of each component of the gear pump should be reasonably selected. That is to say, when conveying different media, a gear pump should be reasonably selected based on the characteristics of the media. So, how can we improve the service life of the gear pump? Below, we will introduce the different classifications of gear pumps mentioned above one by one1. Cast iron gear pump
Cast iron gear pump is mainly suitable for lubrication, viscosity below 1500cst, medium without solid particles, and temperature below 80 ℃.
. In working conditions like this, the service life of conventional gear pumps is generally longer, usually 3-5 years. As time goes on, the pressure of the gear pump will decrease, the flow rate will decrease, and there will be leakage and other phenomena in the seal. In severe cases, it may not be able to pump oil. This situation basically belongs to normal wear of gear pumps. Especially when conveying lubricating grease media, some media may not be very clean, while others may contain small particles, such as residual oil, reused oil, heavy or light fuel used for boiler combustion. If you want to improve the service life of gear pumps on the basis of conventional gear pumps, then start from the following points; (1) Change the gear material of the gear pump from conventional 45 material to 40Cr material, and perform quenching and tempering treatment. (2) The gear pump thrust plate has been changed from cast iron material to cast steel material. (3) The shaft sleeve has been changed from the original steel back composite sleeve to stainless steel shaft sleeve or silicon carbide shaft sleeve2. Stainless steel gear pump
The selection of stainless steel gear pump mainly depends on the corrosion characteristics of the medium conveyed by the gear pump and the requirements for hygiene.
. The common problem with stainless steel gear pumps is that the material does not meet the standard, resulting in a short service life or inability to use the gear pump at all. To improve the service life of stainless steel gear pumps, the selection should be accurate according to different working conditions, and the quenching and tempering treatment methods for each component should be reasonable3. High temperature gear pump
High temperature gear pump, as the name suggests, is a gear pump that delivers medium with higher temperatures.
. If the temperature of the gear pump is between 150 degrees, ordinary ductile iron can be selected. Cast steel material should be selected between 150 degrees and 250 degrees, and stainless steel material should be selected above 250 degrees. When selecting the material, the overall density of the casting or forging should be considered. It is recommended to choose forgings for processing of high-temperature gear pumps. Graphite packing, carbon fiber packing, mechanical seals, or corrugated pipe mechanical seals are commonly used for sealing[2] Leakage treatment during installation and static testing of stainless steel gear pumps
Occasionally, stainless steel gear pumps may experience sealing leakage during use, and there are different repair errors for sealing leakage under different media conditions.
. Let's take a look at the sealing leakage phenomena in various situations1. Leakage during installation and static test of stainless steel gear pump:
After the mechanical seal of the gear pump is installed and debugged, a static test is generally required to observe whether the leakage is large or small.
. If the leakage is small, it may be a problem with the sealing ring of the dynamic or static ring. If the leakage is large, it indicates a problem with the friction between the dynamic and static rings. On the basis of preliminary observation of the leakage amount and judgment of the leakage location, manual turning observation is carried out. If there is no significant change in the leakage amount, there is a problem with the static and dynamic ring seals. For example, if there is a significant change in the leakage amount during turning, it can be concluded that there is a problem with the friction between the dynamic and static rings. If the leakage medium sprays along the axial direction, there are mostly problems with the dynamic ring seals. If the leakage medium sprays around or leaks out from the water cooling hole, it is mostly a failure of the static ring seals. In addition, leakage channels can also exist simultaneously 2. Leakage during the trial operation of stainless steel gear pump: After the mechanical seal of the stainless steel gear pump has undergone static testing, centrifugal force will be generated during high-speed rotation, which will affect the leakage of the medium. Generally, it is caused by the friction between the dynamic and static rings, and the corresponding measures are mostly to disassemble the pump and replace the seal 3. Sudden leakage during normal operation of stainless steel gear pump: Due to significant changes in working conditions or improper operation and maintenance, it is possible to cause sudden leakage during the operation of stainless steel gear pump. Evacuation, cavitation, or prolonged pressure holding can lead to seal damage, resulting in a smaller actual output of the pump. A large amount of medium circulates inside the pump, accumulating heat, which can cause gasification of the medium, leading to seal failure. For long-term shutdowns and restarts without manual turning, friction can tear the sealing surface due to adhesion; An increase in corrosive, polymeric, and cementitious substances in the medium; Sudden changes in ambient temperature, etc Sudden leaks during operation are mostly caused by significant changes in operating conditions or improper operation and maintenance. 1. Evacuation, cavitation, or prolonged pressure holding can cause seal damage. 2. The actual output of the pump is too small, and a large amount of medium circulates inside the pump, causing heat accumulation. Causing the medium to vaporize and causing seal failure 4. The stainless steel gear pump was shut down for a long time, and when restarted, there was no manual turning, causing friction and tearing of the sealing surface due to adhesion 5. The corrosive, polymeric, and cementitious substances in the medium transported by stainless steel gear pumps increase 6. The temperature of the medium or the environment being transported by the stainless steel gear pump changes rapidly. 7. Pay more attention to the maintenance and operating conditions of the pump in daily life, which can cause the sealing O-ring to fail and cause pump leakage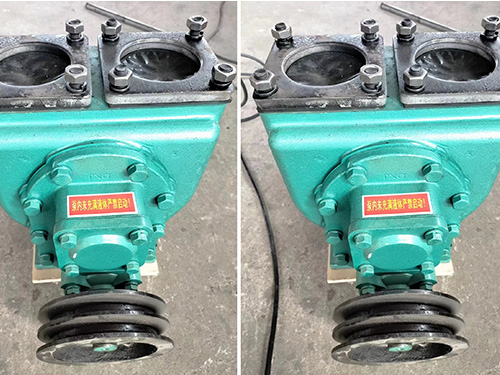
The YHCB high flow pump has the characteristics of large flow rate, high head, small settli...
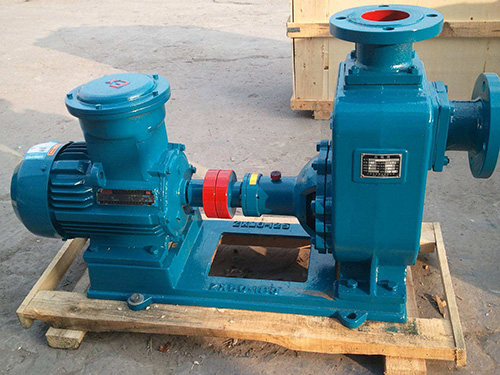
The CYZ centrifugal pump adopts an axial return liquid pump body structure, which is compos...
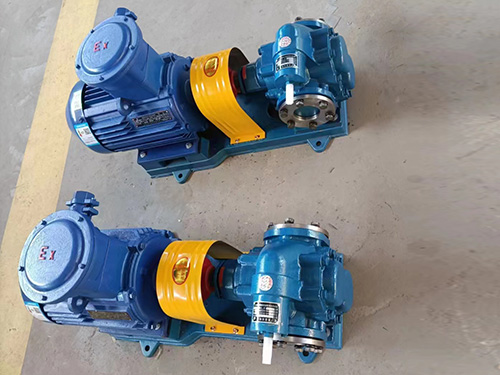
Copper gear pump (KCB type) is suitable for conveying lubricating oil or other liquids with...
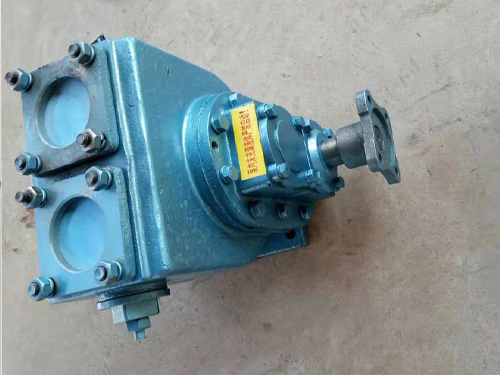
The car mounted circular arc gear pump can be installed on the car and driven by the output...