The relationship between assembly clearance and service life of gear pump
2025-07-09 08:57:19
The assembly clearance of gear pumps is closely related to their service life, and reasonable clearance design is a key factor in balancing the performance and service life of pumps. The following is a detailed analysis of the relationship between the two:
1. The influence of assembly clearance on the service life of gear pumps
1) Radial clearance (clearance between tooth tip and pump casing)
Too small gap:
Causing increased friction between the gear and the inner wall of the pump casing, resulting in wear and heat generation, and shortening the life of the bearings and gears. Possible gear pump seizure caused by thermal expansion or impurity jamming
Excessive gap:
Increase internal leakage (reflux from high-pressure area to low-pressure area), reduce volumetric efficiency, require higher speed compensation flow, indirectly accelerate wear.
When the viscosity of the medium is low (such as light oil), the leakage is more significant, and long-term operation leads to a continuous decrease in efficiency.
2) Axial clearance (clearance between gear end face and side plate)
Too small gap:
The end face friction increases, especially under high pressure conditions, and the side plate or gear end face is prone to burning (such as when in metal metal contact).
Sensitive to temperature, thermal deformation may cause gaps to disappear.
Excessive gap:
The axial leakage path widens, making it difficult to establish pressure and reducing efficiency; In extreme cases, the pump cannot output the rated pressure.
3) Tooth flank clearance (meshing tooth clearance)
Too small gap:
Tight gear meshing can increase friction and result in severe tooth wear. Sensitive to assembly errors, which can easily lead to local stress concentration.
Excessive gap:
Although reducing meshing friction, it will exacerbate flow pulsation and noise, and long-term impact loads will reduce bearing life.
2. Optimization objectives for reasonable gaps
Maximum lifespan conditions:
The radial/axial clearance must ensure:
Dynamic lubrication film formation (approximately 0.02~0.05mm under mineral oil conditions).
Compensate for thermal expansion (the gap should be appropriately enlarged under high temperature conditions).
The backlash between teeth should meet the requirement of elastic deformation compensation (such as avoiding interference during gear micro deformation under heavy load).
Material and working condition adaptation:
Steel wheels, copper wheels, stainless steel wheels, etc. require strict control of clearance, while nylon wheels can be slightly loose (due to differences in thermal expansion coefficients).
3. Typical failure modes caused by abnormal assembly clearances
Early wear: Insufficient clearance → Poor lubrication → Direct metal contact → Adhesive wear (such as pulling the tooth surface).
Fatigue failure: excessive clearance → flow pulsation → bearing subjected to alternating load → bearing peeling or fracture.
Sudden efficiency drop: Internal leakage exceeding the limit (such as when the axial clearance wear exceeds 0.1mm, the efficiency may decrease by more than 30%).
4. Practical suggestions for extending lifespan
1. Dynamic gap control:
Using floating side plates or adjustable gaskets to automatically/manually compensate for clearance after wear (such as common designs for external gear pumps).
2. Lubrication optimization:
High viscosity oil can appropriately enlarge the gap, but the Reynolds number needs to be checked to avoid laminar flow failure.
3. Working condition matching:
When conveying media containing particles, the gap should be greater than the maximum particle size (such as the design standard ISO 13709 for chemical pumps).
4. Assembly process:
Adopting hot assembly (heating pump body) to ensure uniform cold clearance and avoid eccentric wear caused by forced centering.
Comparison of lifespan:
When the axial clearance increases from 0.05mm to 0.15mm, the volumetric efficiency decreases by 20% and the lifespan may be shortened by 50% (depending on the load).
conclusion
The assembly clearance of gear pumps needs to strike a balance between reducing leakage and minimizing friction. By precise design, material selection, and working condition adaptation, the clearance can be controlled within the optimal range, significantly extending the service life
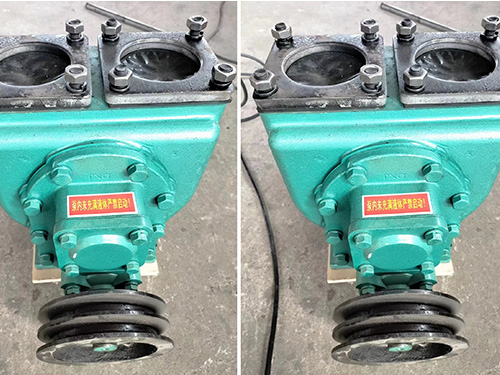
The YHCB high flow pump has the characteristics of large flow rate, high head, small settli...
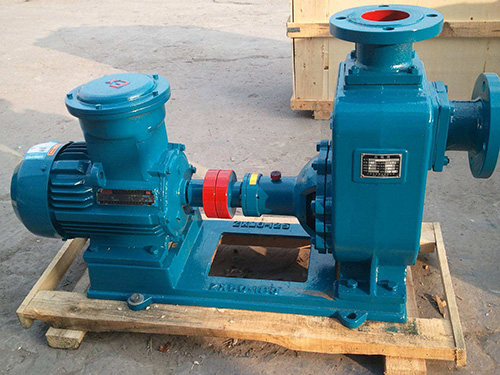
The CYZ centrifugal pump adopts an axial return liquid pump body structure, which is compos...
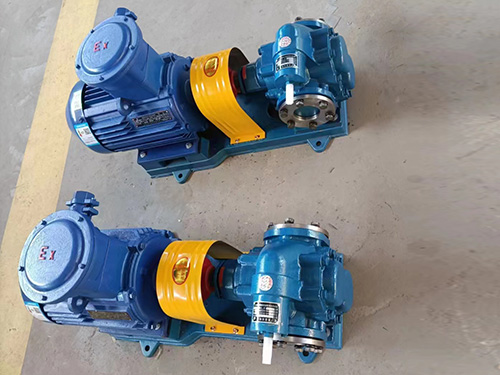
Copper gear pump (KCB type) is suitable for conveying lubricating oil or other liquids with...
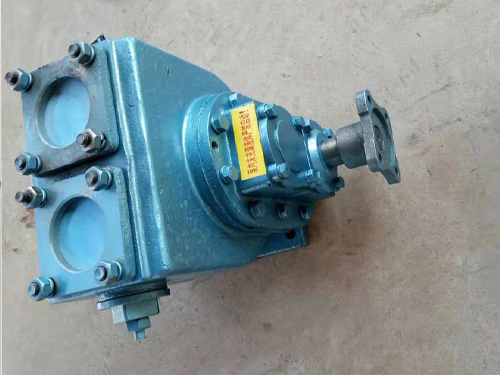
The car mounted circular arc gear pump can be installed on the car and driven by the output...