How to solve the problem of high viscosity pump noise
2024-04-15 08:55:19
The level of noise during the transportation of a high viscosity pump depends on various factors such as the viscosity of the medium, the diameter of the pipeline in the high viscosity pump, the length of the pipeline, and the resistance of the pipeline. High viscosity pumps are common causes of noise in fluid conveying systems, including changes in liquid flow velocity, flow rate, and pressure, bubble rupture, and alternating loads. Gear pumps that transport high viscosity liquids are the main source of system noise.
Reasonably determining the working speed of a high viscosity pump to avoid meshing resonance frequency between the gear and shaft rotation can prevent increased noise. Because resonance is prone to occur when the meshing frequency is close to the natural frequency of the gear system. The use of appropriate isolation techniques can prevent vibration from being transmitted to adjacent structures. For this purpose, the pump and the drive motor should be connected through a flexible coupling and installed on the same bottom plate with coaxiality. The bottom plate should be installed on an elastic support to further improve the vibration isolation effect. Setting an expansion chamber or accumulator on the outlet pipeline of the pump to absorb the pressure pulsation of the pump or buffer the sudden pressure change in the pipeline is a means of controlling the noise of high viscosity gear pumps.
Installation and commissioning of high viscosity pumps
The support or flange of a high viscosity gear pump and its driving motor should adopt a common installation foundation, and the foundation, flange or support should have sufficient stiffness to reduce the vibration and noise generated during the operation of the gear pump. The electric motor and pump must be connected by an elastic coupling, with a coaxiality of less than 0.1 millimeters and a tilt angle not exceeding 1 degree. When installing the coupling, do not use a hammer to strike it to avoid damaging the gears and other parts of the gear pump. If driven by pulleys, sprockets, etc., a bracket support should be provided to prevent radial force on the driving gear bearings. When tightening the anchor screws of the gear pump and motor, the screws should be evenly stressed and connected. When turning the coupling by hand, it should be felt that the gear pump can rotate easily without any abnormal phenomena such as jamming, before piping can be done. The inner diameter of the oil suction pipeline for high viscosity pumps should be large enough to avoid narrow passages or sharp bends, reduce bends, remove unnecessary valves and accessories, lower the installation height of the pump as much as possible, shorten the length of the oil suction pipeline, and reduce pressure loss. The sealing of components such as pipe joints should be good to prevent air intrusion and control the occurrence of cavitation and erosion.
Before starting the operation of the high viscosity oil pump, fill the housing of the gear pump with the liquid to be transported for easy start-up. If the ambient temperature is below freezing point, hot steam should be introduced into the pump in advance for preheating treatment before starting the pump. The rotation direction of the pump should match the inlet and outlet ports. If the high viscosity internal gear pump is operated for the first time or is idle for a long time before use, it is better to run for about an hour under no-load or low load conditions. If abnormal temperature rise, leakage, vibration, and noise are detected in advance during the running in phase, the machine should be stopped for inspection.
It is better to install a check valve and a protective valve on the output pipeline of the gear pump. In this way, when repairing the pump and output pipeline, the liquid in the system will not backflow. When the pump is stopped under load, it can also prevent the pump from reversing and generating local vacuum in its output pipeline. It should be noted that the outlet check valve cannot be installed upside down or stuck. Protective devices such as protective valves should also be installed on the outlet pipeline of high viscosity pumps, so that once the outlet channel of the pump is blocked, the protective valve can be opened to relieve pressure. The protective valve can be integrated with the pump body or pump cover, or can be assembled separately. For high viscosity gear pumps that require forward and reverse rotation, protective valves must be installed on both the inlet and outlet pipelines.
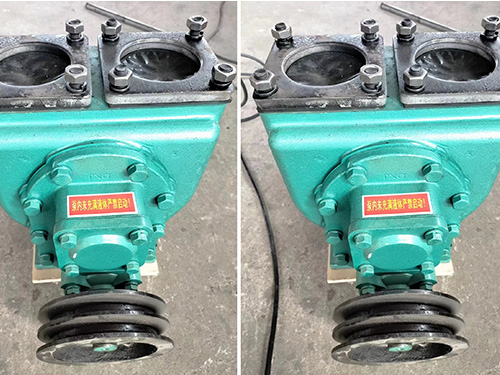
The YHCB high flow pump has the characteristics of large flow rate, high head, small settli...
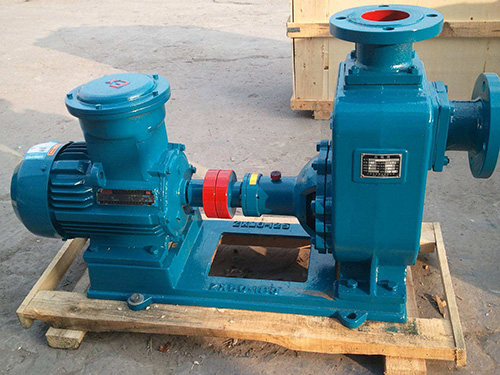
The CYZ centrifugal pump adopts an axial return liquid pump body structure, which is compos...
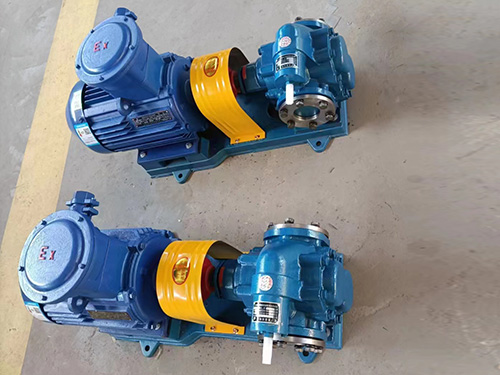
Copper gear pump (KCB type) is suitable for conveying lubricating oil or other liquids with...
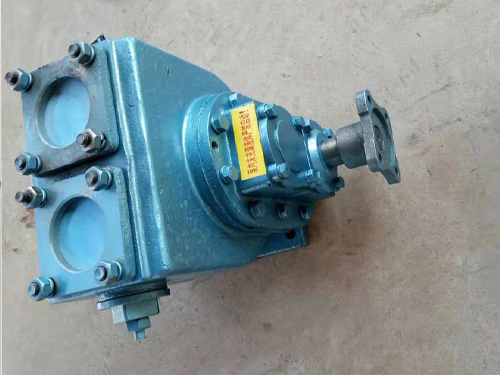
The car mounted circular arc gear pump can be installed on the car and driven by the output...